目录
In fluid systems across industries, from manufacturing plants to HVAC systems, cleanliness isn’t just a luxury. It’s essential. Magnetic filters play a silent but critical role in maintaining cleanliness, capturing metallic contaminants before they damage pumps, clog valves, or corrode sensitive equipment.
Without an effective filtration method, metal shavings, rust, and other iron-based debris can circulate through your systems. This can lead to costly maintenance, decreased performance, and unexpected breakdowns. Magnetic filters help you avoid these problems by capturing ferrous particles before they do any damage.
These filters serve as frontline protection for precision equipment. Without them, even microscopic metallic particles can reduce efficiency, clog components, and shorten the lifespan of your systems. They are simple in concept but essential in application.
But what are magnetic filters really made of? How do they work? And what should you look for if you’re sourcing them for your business? This guide lays out everything you need to know, from structure to sourcing.
What is a Magnetic Filter?
A magnetic filter is a device designed to remove ferrous particles from liquids and gases. These filters use high-intensity magnets, typically neodymium or ferrite, to attract and trap iron-based contaminants.
They work passively. As fluid flows past the magnetic core, ferrous debris is pulled out of the stream and held against the magnet. This simple mechanism prevents metal fragments from circulating and causing damage.
Magnetic filters are commonly installed in pipelines, processing tanks, and cooling circuits. Their job is simple: remove metal debris before it causes abrasive wear, clogs, or mechanical failure.
The filters act without external power and continue to function under a wide range of pressures and temperatures. That versatility makes them suitable for nearly every industry dealing with fluids.
Unlike traditional filters, they don’t rely on mesh or paper elements. That means no clogging and no frequent replacements, making them ideal for systems requiring consistent flow.
They are especially useful in environments where traditional filters either fail quickly or require constant replacement. Because they work with zero energy input, they are efficient and extremely cost-effective over time.
Their effectiveness extends to particles that would otherwise escape mesh filters, offering superior protection in fine filtration scenarios.
How Are Magnetic Filters Made?
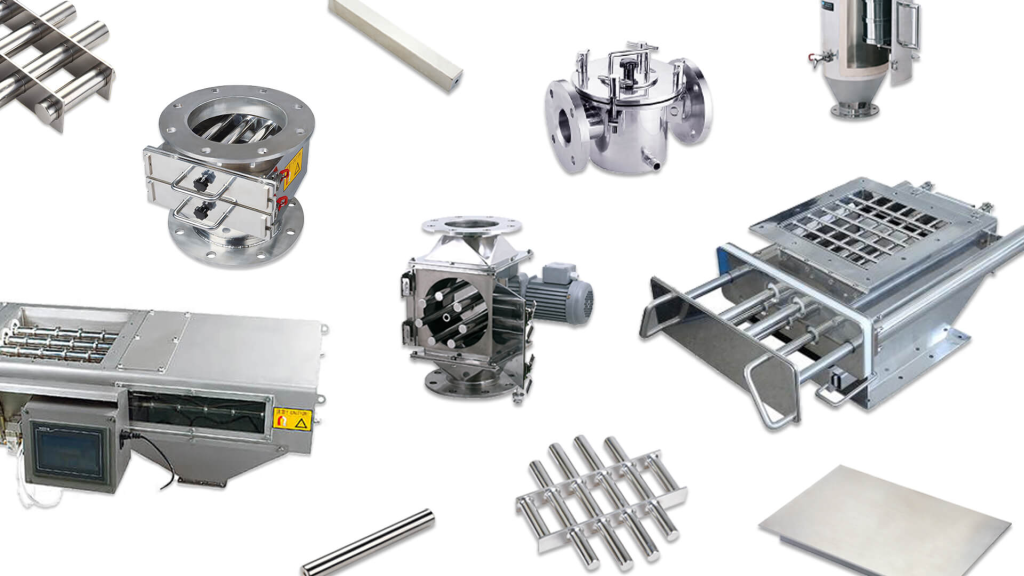
The heart of any magnetic filter is its magnetic core. Most high-performance units use rare-earth neodymium magnets because of their strong pull force and thermal stability.
These magnets are exceptionally powerful and retain their magnetism over time. They are ideal for harsh industrial conditions where both strength and durability are required.
The magnets are usually shaped into rods or bars, which are then arranged to maximize exposure to flowing fluids. The arrangement varies depending on the design—linear, radial, or grid-based layouts are all common.
Strategically positioning these magnets ensures better capture rates. Some designs focus on maximizing dwell time the amount of time particles are exposed to the magnetic field.
This design increases the surface area where ferrous particles can be captured, improving overall filtration performance. Some filters are modular, allowing users to scale capacity depending on contamination levels.
The magnets are encased in housings made of stainless steel or other corrosion-resistant metals. The design ensures that contaminants stick to the magnetic surface without breaking the flow path.
Materials used in these housings are often chosen for their compatibility with the fluid being processed, whether corrosive, food-safe, or pressure-sensitive.
Some filters include purge valves or mechanical scrapers for self-cleaning. These advanced units allow for continuous operation without stopping the system for maintenance.
In high-sanitation environments like food or pharma, filters must also meet hygiene standards. That means smooth welds, sealed joints, and FDA-compliant materials.
Additional treatments such as passivation or electropolishing may be used to further enhance surface hygiene and corrosion resistance in sensitive applications.
Each filter is engineered for durability, longevity, and precise functionality—making manufacturing quality a critical factor.
Types of Magnetic Filters
Magnetic Rods (Bars)
These are single solid magnetic cores typically installed in tanks, pipes, or housings. Their cylindrical shape allows them to fit into various systems without significantly disrupting flow.
Rod magnets are often used in hopper applications or gravity-fed chutes, where they trap metallic particles before they move downstream.
Magnetic Grates (Grids)
Grate filters consist of multiple magnetic rods arranged in parallel or crosswise layouts. This configuration creates a magnetic field grid that captures more particles over a broader surface.
They’re commonly installed at the entry points of process lines to intercept contamination early. Grids are especially effective for dry materials and powders.
Inline Magnetic Filters
These filters are placed directly into the fluid line, featuring an enclosed body that houses magnets. They’re compact, easy to install, and highly efficient for capturing particles during fluid transport.
Inline filters are often built to withstand pressure, temperature changes, and corrosive fluids. They’re perfect for closed-loop systems.
High-Intensity Liquid Traps
These are heavy-duty, fully sealed filters made to handle viscous fluids such as syrups, oils, or adhesives. The strong magnetic fields catch extremely fine ferrous particles.
They are used in industries with strict hygiene requirements and in high-viscosity product lines that demand uncompromised cleanliness.
Self-Cleaning Magnetic Filters
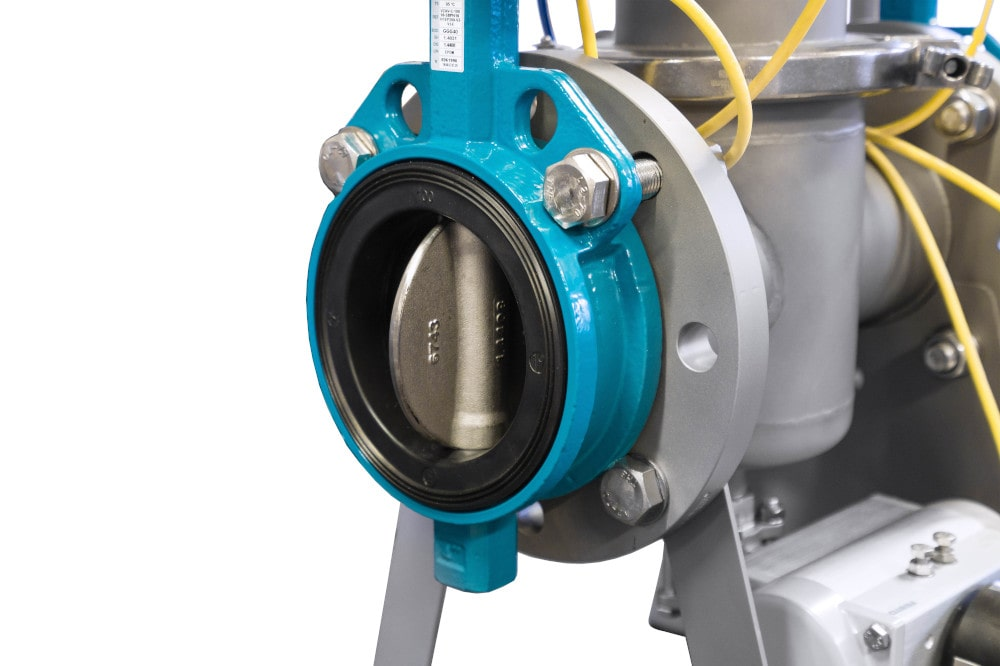
Automated filters that mechanically scrape magnetic rods and remove captured debris without halting operations. These reduce labor costs and improve system uptime.
They’re ideal for 24/7 production environments like chemical plants or heavy-duty manufacturing where efficiency is critical.
Magnetic Filter Bags and Sleeves
These are fabric housings embedded with magnets. They’re more flexible and can be used in applications with limited space or irregular shapes.
While not as powerful as rigid units, they provide lightweight, temporary filtration solutions and are often used in batch or pilot-scale systems.
What Are the Advantages of Magnetic Filters?
No Disposable Media
Magnetic filters don’t require replacement cartridges or disposable filter media. This drastically cuts down on ongoing operational costs.
Over time, the absence of consumables translates to lower environmental impact and simpler maintenance routines.
High Efficiency
They can capture particles down to sub-micron sizes, including particles too small to see with the naked eye. This makes them particularly useful in precision environments.
The strength of neodymium magnets ensures that even fast-moving contaminants are intercepted before they cause damage.
Consistent Flow
Because they don’t clog like mesh or fiber filters, magnetic filters maintain steady flow rates. This reduces pressure drops and keeps systems running at optimal performance.
Uninterrupted flow also means fewer system checks, lower energy costs, and reduced stress on pumps.
Equipment Protection
By trapping abrasive metallic particles, magnetic filters reduce mechanical wear on critical components like valves, seals, and bearings.
This leads to fewer repairs, lower replacement part costs, and extended service intervals for machines.
Long Service Life
Magnets rarely lose strength and stainless steel housings resist corrosion. A well-built magnetic filter can last for years with minimal upkeep.
This durability makes them a cost-effective investment with high returns across multiple production cycles.
Environmentally Friendly
The reusable nature of magnetic filters makes them a greener option. With no cartridges to dispose of, they align with sustainability goals.
Companies aiming for zero-waste or ISO 14001 compliance find magnetic filters support their environmental benchmarks.
Cost Effective
Initial installation may cost more, but the long-term savings on maintenance, downtime, and replacement parts often outweigh the upfront expense.
ROI is realized quickly in high-usage environments, where performance and reliability are paramount.
Applications of Magnetic Filters
Industrial Machining & CNC
Used in coolant and lubrication systems, magnetic filters prevent metal fragments from circulating, protecting tools and machinery.
They improve surface finish quality and reduce wear, leading to higher productivity and longer machine life.
Food & Beverage Processing
Magnetic filters help eliminate metal particles from ingredients or final products, ensuring food safety and compliance with regulations.
In beverage lines, they are used to safeguard filling equipment and maintain hygiene standards.
HVAC & Boiler Systems
Iron oxide sludge in heating systems can cause major efficiency losses. Magnetic filters help capture these particles and keep systems running smoothly.
They are commonly used in residential and commercial heating to extend boiler lifespan and reduce energy consumption.
Pharmaceutical & Cosmetics
Precision is everything in these sectors. Magnetic filters remove microscopic metallic debris that could compromise product purity.
They’re often integrated into mixing tanks, transfer lines, and final filling systems to maintain GMP standards.
Oil & Gas Refining
In upstream and downstream applications, magnetic filters remove scale, rust, and weld slag that can damage pumps and metering systems.
This filtration improves throughput, extends equipment life, and prevents costly process interruptions.
Water Treatment Plants
Used to remove rust, iron oxide, and other metallic particles before water reaches membranes or UV systems.
They enhance the performance of secondary filtration stages and reduce the need for chemical treatments.
Additive Manufacturing
Metal powders used in 3D printing must be ultra-clean. Magnetic filters ensure only high-purity materials are used in printing.
This results in stronger parts, better print resolution, and fewer failed builds.
Important Indicators for Testing the Quality of Magnetic Filters
Magnetic Strength (Gauss Rating)
Industrial-grade magnetic filters typically range from 8,000 to 12,000 gauss. This determines how small and how fast particles can be captured.
A higher gauss rating is crucial for fine filtration in high-precision or high-flow environments.
Pull Force
This refers to the actual gripping power of the magnet on particles. It ensures that even under turbulent flow, particles remain attached to the magnetic core.
Systems with high flow velocity or vibration require strong pull force to prevent dislodging of captured debris.
Pressure Drop
High-quality filters should offer minimal resistance to flow. Excessive pressure drop can strain your pump and reduce system efficiency.
Well-designed filters balance particle capture with smooth, uninterrupted flow.
Operating Temperature and Pressure
Not all filters are built for high heat or extreme pressure. Make sure the materials and magnets are rated for your system’s conditions.
For example, rare-earth magnets can lose effectiveness at high temperatures unless specially coated or alloyed.
Debris Holding Capacity
How much material the filter can hold before needing to be cleaned. Larger or modular filters typically have greater holding capacity.
Knowing this helps you predict cleaning intervals and minimize unplanned downtime.
Build Materials and Certifications
Look for filters made of stainless steel (304 or 316) and those that meet ISO, CE, or FDA standards, depending on your application.
Certifications guarantee product consistency and compatibility with industry requirements.
Cleaning Mechanism
Manual units should allow for easy disassembly and cleaning. Self-cleaning units should reliably purge debris without leaks.
Ease of cleaning reduces downtime and improves worker efficiency, particularly in continuous operations.
Where to Import Magnetic Filters?
Global Market Overview
The magnetic filter market is expected to surpass $18 billion globally by 2030. Growth is driven by automation, sustainability, and the demand for equipment longevity.
This rising demand spans manufacturing, water treatment, healthcare, and energy, with Asia-Pacific leading in volume and innovation.
Top Exporting Countries
中国 dominates exports due to its manufacturing scale and price competitiveness. It offers everything from budget options to premium models.
Japan focuses on precision and quality assurance. Japanese filters are preferred in pharma, electronics, and food processing.
Germany is renowned for engineering excellence. German filters are robust, long-lasting, and compliant with strict EU standards.
USA exports include custom-engineered filters backed by strong customer service and compliance support.
India and South Korea are growing players offering cost-effective alternatives with improving quality metrics.
Top Importing Regions
The U.S., EU, and Southeast Asia are major consumers. Rapid industrial growth in Vietnam, Indonesia, and Thailand is also increasing demand.
Importers typically prioritize technical support, local regulation compliance, and after-sales service when selecting suppliers.
When sourcing filters, ask for technical data sheets, certifications, sample units, and service agreements.
结论
Magnetic filters are an essential tool in modern industrial and commercial systems. They protect equipment, maintain fluid cleanliness, and reduce operational costs across a wide range of applications. Their long life, zero-waste operation, and consistent performance make them a wise choice for companies focused on efficiency and sustainability.
When choosing a magnetic filter, consider the type of system, fluid characteristics, and operational environment. Look beyond price and focus on performance indicators like magnetic strength, flow rate, and maintenance needs. If you’re planning a system upgrade or exploring new installations, magnetic filters are a smart, sustainable, and cost-effective solution.