Table of Contents
Neodymium Iron Boron (NdFeB) magnets, today considered to be the strongest permanent magnets, have become widely applied in industries such as electronics, automotive, renewable energy, and health care.
Their only weakness, despite being so powerful magnets, is that they are very susceptible to corrosion and oxidation, especially under humid and chemically aggressive environments. That’s why NdFeB magnet coating is so important.
Coating provides time preservation of magnetic properties, enhanced durability, better performance, and safety in different applications. Indifference towards a proper coating results in fast deterioration of these magnets and thus translates into reduced functionality or even failure of critical components.
This review aims to explore different types of coatings available for NdFeB magnets, compare their performances, and choose the best one in terms of an application. Coating processes, advantages of applying coating, and future trends affecting the critical aspect of magnet technology will also be discussed.
Part 1: Common Coating Materials for NdFeB Magnets
NdFeB magnets are highly reactive to environmental factors like moisture and oxygen, which will soon corrode their surfaces and magnetic integrity. These coatings are applied to avoid this kind of deterioration.
Well-known coatings are the following for NdFeB magnets:
Nickel (Ni-Cu-Ni) Coating
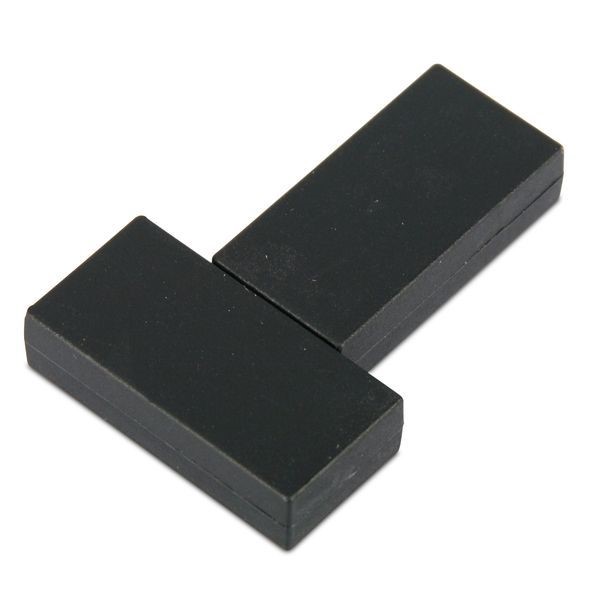
Nickel is the most-used coating material. This is because nickel has the best characteristic of corrosion resistance associated with strength and attractiveness. Normally, this coating is done in a tri-layer (Nickel-Copper-Nickel) on a longer, shiny metallic look finish.
The first two of such three layers of Nickel protect against corrosion and wear, while the copper middle adds both adhesion and flexibility. The design is for general industrial uses, for electronics, as well as those proposed to consumers alike.
Epoxy Coating
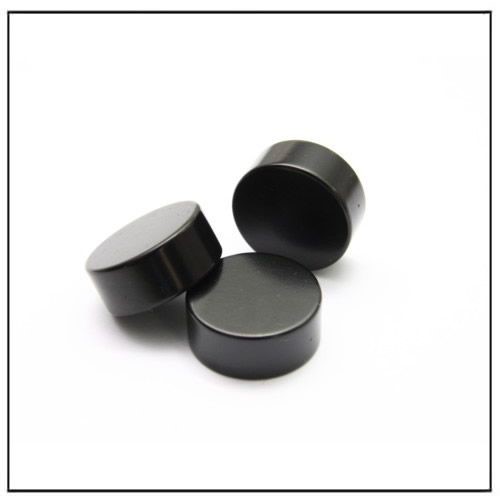
Epoxy is the ultimate type of protection in humid, wet, or chemically aggressive environments. This non-metallic coating forms a thick, protective skin that resists moisture, salt spray, and chemical corrosion.
They come in various colors such as black, grey, and even custom color formulations to fit the application that requires protection and the eye. With regard to mechanical strength, epoxy is less significant when compared to metal coatings, but this makes it suitable for marine, automotive, and outdoor applications.
Zinc (Zn) Coating
Zinc coatings come cheap above all. It provides moderate corrosion resistance and it’s very easy to apply, either by electroplating or mechanically. Zinc mostly acts as a sacrificial coating: it will corrode first before the magnet itself would do so.
Though they are not very well suited for very harsh environments, Zn coatings could be selected quite often for low-risk indoor applications where moisture exposure would be quite limited.
Phosphate Coating
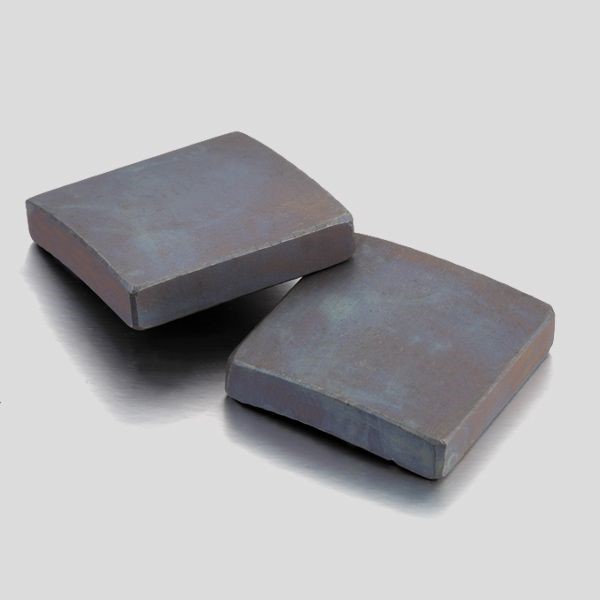
Phosphating is used generally as one of the first coat layers to assist adhesion when painting or applying other coatings. The treatments of phosphate are not very resistant to corrosion, though they may slightly contribute to increasing surface roughness.
Gold (Au) Coating
The applications for gold coatings are very special. Most applications are found in medicine and aerospace. Gold is inert, biocompatible, and has extreme resistance to corrosion, making it the perfect element for implants or devices that are going to see body fluids or harsh chemicals.
Gold itself is extremely costly, and therefore it is used only in those situations where its unique properties are most crucial.
Parylene Coating
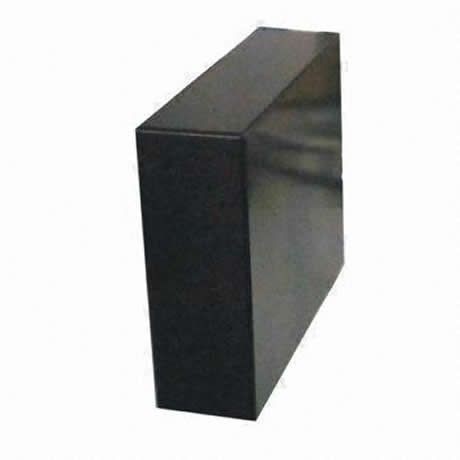
Parylene is a polymer coating produced by chemical vapour deposition. It allows this barrier to be formed extremely thin and without pinholes, without interacting with the substrates.
The barrier is remarkably resistance to moisture, chemicals, and temperature. Typical applications of parylene coatings are for electronic, medical, and aerospace components requiring precision and reliability.
Part 2. Introduction to the Performance of Commonly Used Coating Materials
Here’s a quick overview of how these materials perform in key areas:
Coating Material | Corrosion Resistance | Mechanical Strength | Thermal Stability | Cost | Common Use Cases |
Ni-Cu-Ni | High | High | Moderate | Moderate | General-purpose, electronics |
Epoxy | Very High | Moderate | Low to Moderate | Low | Marine, outdoor use |
Zinc | Moderate | Moderate | Low | Low | Low-risk environments |
Phosphate | Low | Low | Low | Very Low | Pre-treatment layer |
Gold | Very High | Moderate | High | High | Medical, aerospace |
Parylene | Excellent | Moderate | High | Very High | Precision electronics |
Part 3. How to Choose the Coating Material of NdFeB Magnets?
Rightly popular is that NdFeB magnets must yield a definite compulsory coating material in the maintenance of integrity and performance for different applications. The necessary protection against corrosion and wear via efficient choice of NdFeB magnets coating should also preserve compatibility with mechanical, thermal as well as environmental demands.
Here are some of the factors to consider when choosing a coating material:
Environmental Exposure
Among other factors, the operational surroundings can be said to be the most significant in deciding for NdFeB magnets the coating to be used.
Under dry indoor conditions with low moisture or chemical exposure, a standard Nickel-Copper-Nickel (Ni-Cu-Ni) coating can be called upon to do the trick. It serves good corrosion action but has a top-notch metallic glare that makes it fit for consumer electronics and simple industrial use.
If the magnets are to be exposed to outside conditions, or in environments transporting high humidity or salt-like marine conditions, then a more robust coating would be required. Most moisture-resistant epoxies should be reliable; otherwise, parylene delivers a completely sealed, pinhole-free surface.
Mechanical Wear and Handling
NdFeB magnets that are dynamic or found in high-friction environments need specially protective coatings against physical damage. Nickel coatings are pretty good in applications where handling, mechanical impact, or entanglement into a mechanical system is present, as they have great hardness and high wear resistance.
On the other hand, in instances wherein the magnet does not encounter heavy mechanical forces but needs environmental exposure protection during installation, epoxy might be an advisable option. It does not have the same degree of mechanical robustness as metals, but it offers above-average protection and adapts readily to applied difficult shapes.
Temperature Tolerance
The operating temperature is another significant factor to be considered under the NdFeB magnets coating. The heat is highly detrimental to these magnets, and a few moments of heat exposure would cause their permanent demagnetisation.
The coatings would not stop demagnetisation of the magnet, yet would keep the surface of the magnet safe from thermal oxidation. Nickel and gold coatings show stability at moderately high temperatures and preserve good structural integrity.
On the other hand, the epoxy coatings have very limited tolerance to heat, degrading or softening at elevated temperatures, such that they cannot be used for high-heat applications. Parylene, deposited by vapour deposition, has excellent thermal stability and is to be treated as outstanding in environments at high temperatures.
Electrical and Functional Requirements
For coatings used in electronics or medical device applications, electrical and biological characteristics must be met. Coatings like epoxy and parylene are good insulators. This property makes them suitable for magnet applications in electronics, where electrical shorts need to be avoided.
Parylene is especially good for applications in precision electronics and aerospace due to its ability to provide very thin and uniform coatings. In the biomedical area, gold and parylene are biocompatible/non-toxic and can be used safely in internal medical devices or instruments that come into contact with biological tissue.
Cost and Budget Constraints
The budget for coating NdFeB magnets is practical but an absolute necessity. When cost-modelling is important, zinc or phosphate coatings give basic protection at the lowest cost, suitable for indoors in a non-critical application.
Nickels are the most frequently used because they are well-balanced in price, corrosion resistance, and durability. In high-end or specialty applications, gold, parylene, and PTFE coatings are used; however, because of the costs, they are generally reserved for mission-critical applications where the performance involved certainly would justify the cost.
Aesthetic Consideration and Customisation Needs
Wherever the aesthetic appearance of the magnet is important in consumer electronics, promotional products, or decorative applications, coatings aesthetic comes into play.
Nickel coatings offer a shiny metallic surface aesthetically pleasing as well as functional. On the other hand, epoxy coatings can be customised in colours and textures, offering alternatives to companies that desire to have their components in line with a certain visual theme.
Part 4. How Are NdFeB Magnets Coated?
Applying a coating to NdFeB magnets is a process of great importance in terms of their longevity and performance properties in various environments. Some well-accepted coating processes for NdFeB magnets are described here.
Electroplating
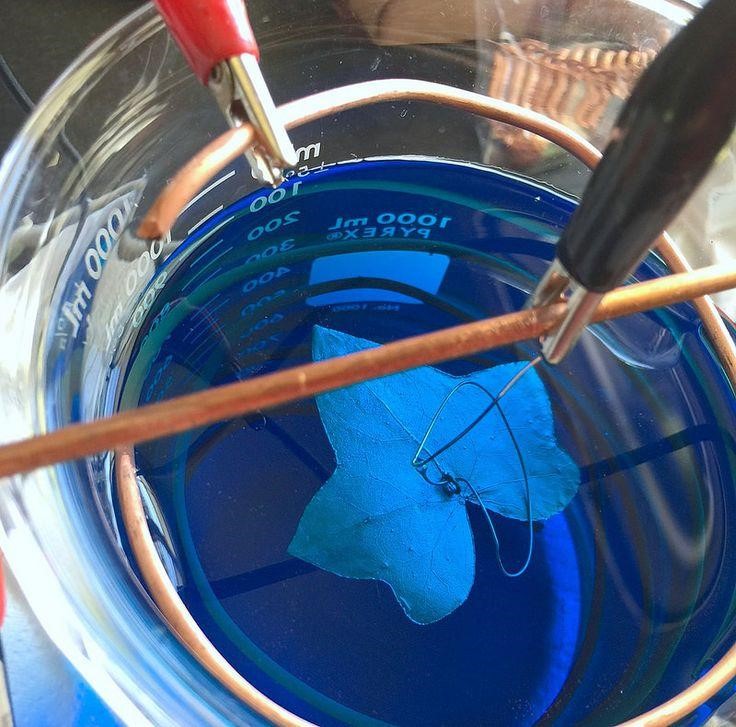
Nickel, copper, or gold are the commonly used metals electroplated on NdFeB magnets. The magnet is dipped in the electrolyte solution, consisting of metal salts, for the electrodeposition process.
One may obtain a very thin and uniform metallic coating having excellent corrosion and wear resistance properties. This is usually electroplated Ni-Cu-Ni, since this coating provides a fair compromise between performance and cost.
Powder Coating
Powder coating enables the application of different forms of non-metal coatings, including some liquids like epoxy. The dry powder is electrostatically charged and then sprayed on the surface of the magnet.
The electrostatically charged particles get attached to the surface by mechanical action and later on are bonded to the surface of the magnet following curing in an oven. This results in the formation of a thick and wear-resistant layer with moisture, chemical and abrasion protection.
Dip Coating
Dip coating is a very simple, very cheap means of getting marine-type epoxy and phosphate coating. The magnet is simply dipped into a solution of the coating, and a homogeneous coating is applied across all surfaces.
If the dipped-in solution is allowed to dry after immersion, it can be repeated to create the required thickness. Generally, dip-coating is used where high precision is not necessary but does require protection from corrosion or environmental attack.
Spray Coating
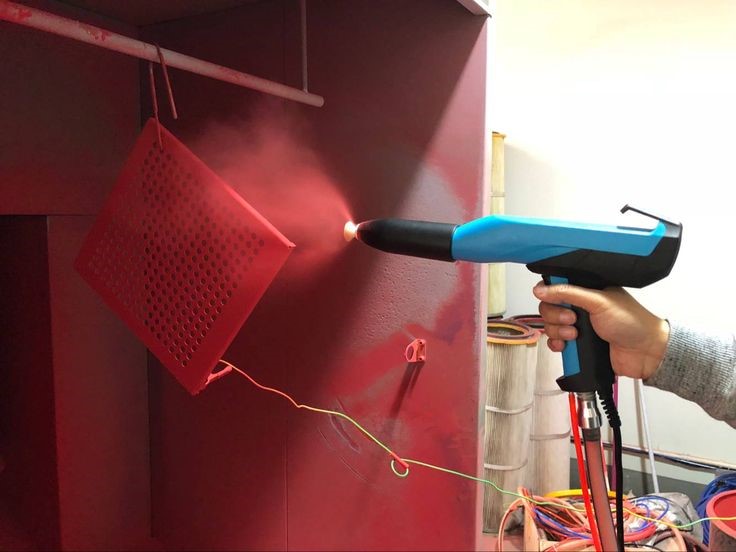
Spray coating is the application of coating material via an airbrush or sprayer, mostly for epoxies or paints. The coating material is atomised into small droplets and sprayed directly onto the surface of the magnet. This technique is often employed where there.
Part 5: What Advantages Does Coating Bring to NdFeB Magnets?
Here are some of the advantages one gets by coating NdFed Magnets:
- Corrosion Protection – Shields moisture and oxygen from rusting magnets.
- Improved Durability – Increases resistance to physical damage while handling.
- Thermal Stability – Protects from high temperatures demagnetisation occurs.
- Chemical Resistance – concerning corrosion in chemical or marine environments.
- More Aesthetic Value – Presents a highly polished, professional look to consumer goods.
- Biocompatibility- Safe for medical implants and surgical tools.
- Electrical Isolation – Prevents short circuits even within close-contact electronic assemblies.
Part 6. The Future Development Direction of NdFeB Magnets Coating
Demand for NdFeB magnets is increasing and will increase in future years for modern technologies including applications in electric vehicles, renewable energy systems, and miniaturized electronics.
Accordingly, there will be a need for improved coating solutions. Future development in this regard will be at enhancing performance, sustainability, and versatility regarding the application of NdFeB magnets coating.
One major thrust would be in the direction of formulating nano-coatings and multi-layered systems that provide excellent protection with little extra weight. These coatings are expected to achieve low ultra-thin multilayer films with a design of corrosion resistance, thermal stability, and wear resistance in environments with high stress within a compact arrangement.
Another one is progress towards environmentally friendly and non-toxic coatings. In addition, since these regulations have tightened, researchers are looking into replacing these hazardous materials with eco-friendly alternatives for use in electroplating processing.
Emerging smart coatings could also be seen as quite promising. This innovation would extend significantly the life of NdFeB magnets under extreme or dynamic environments.
There is also a demand in recent days for customised coating solutions for different industries, e.g., biocompatible coatings for medical devices, heat-resistant coatings for aerospace applications, and so on. Technology continues to progress, and hence, there will be a need for coatings that are tailor-made and flexible.
Conclusion
NdFeB magnets are arguably among the most potent permanent magnets ever known; however, their true potential is realised only when coupled with the right coating to protect them.
As technology advances, so will the requirements for magnetic materials- new frontiers for innovation in coating methods and materials. If you’re working on next-gen electronics, renewable energy systems, or a precision medical tool, then understanding and deciding on coating for NdFeB magnets is critical.