목차
Magnetic grids are essential components in the world of industrial filtration. Designed to trap and remove ferrous metal particles from dry materials such as powders, granules, and other bulk solids, these grids offer a reliable way to improve product purity and protect valuable processing equipment.
From food and pharmaceutical production lines to plastic, ceramic, and chemical processing systems, magnetic grids are widely used in gravity-fed and pneumatic conveying applications. Their low-maintenance design, passive operation, and impressive magnetic strength make them indispensable in environments where cleanliness, compliance, and system integrity matter.
This guide takes a deep dive into magnetic grids: what they are, how they’re made, the different types available, key benefits, performance indicators, and where to source the best models for your operation. We’ll also explore emerging innovations, maintenance tips, case studies, and best practices to help users maximize the life and performance of their magnetic grid systems.
What is a Magnetic Grid?
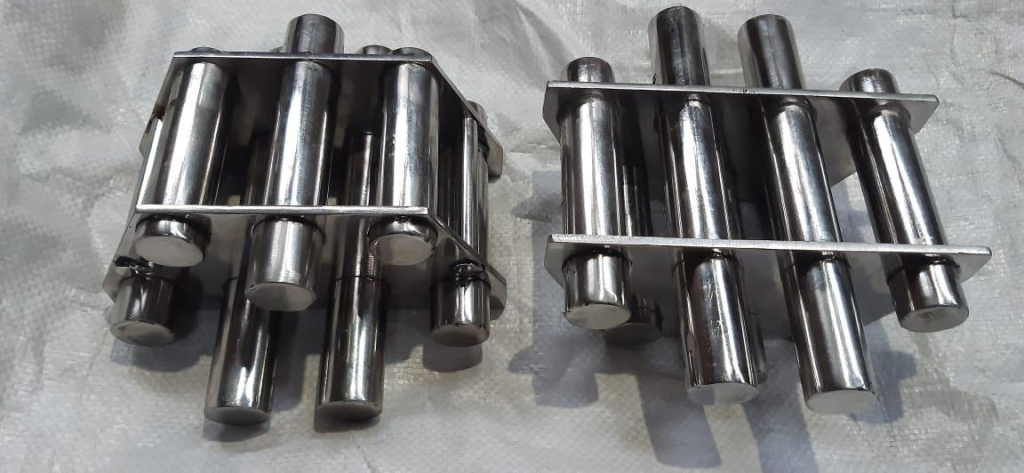
A magnetic grid also called a magnetic grate or grate magnet, is a metal frame fitted with magnetic bars arranged to create a strong magnetic field. These bars capture iron contaminants as material flows through or around the grid.
The goal is to prevent ferrous particles, whether visible metal shards or fine iron dust, from entering downstream processes. These contaminants can damage mixers, extruders, and packaging machines or compromise product quality and safety.
Installed in chutes, hoppers, or bins, magnetic grids are passive systems requiring no electricity or moving parts. As dry material passes over the magnetic field, metal fragments are pulled in and held securely against the rods until manually removed.
Modern grids may also be designed with specialized spacing and orientation to manipulate the direction of flow or to increase dwell time, ensuring maximum particle contact. This flexibility enhances adaptability across diverse product types.
Some newer designs also feature magnetic rods with varying field strengths along their length, offering targeted separation zones within the same grid. This is useful for processing layered or mixed material flows with variable contamination levels.
Magnetic grids are suitable for nearly all industries that handle dry bulk goods from plastics and grains to fertilizers, pigments, or powdered metals. Their design may vary, but their role remains consistent: to protect, purify, and preserve the integrity of materials and machinery.
How Are Magnetic Grids Made?
The construction of magnetic grids involves precision engineering, with a strong emphasis on material quality and magnetic performance.
Magnetic rods are typically made with rare-earth neodymium magnets, sealed inside polished stainless-steel tubes. These tubes are welded shut and pressure-tested to prevent material ingress or corrosion, especially in hygienic environments like food and pharma.
The bars are then mounted within a sturdy stainless-steel frame, arranged in single or multiple layers, depending on the level of protection needed. The entire assembly is fabricated to tight tolerances to ensure uniform spacing and maximum surface contact with passing materials.
For high-performance applications, manufacturers may offer grids with stronger magnet grades (such as N42 or N52), corrosion-resistant coatings, and FDA-compliant finishes. The result is a long-lasting, durable tool built to withstand abrasive flows and harsh cleaning procedures.
Types of Magnetic Grids
Understanding the different types of magnetic grids can help you choose the right one for your operation.
Single-Layer Grids
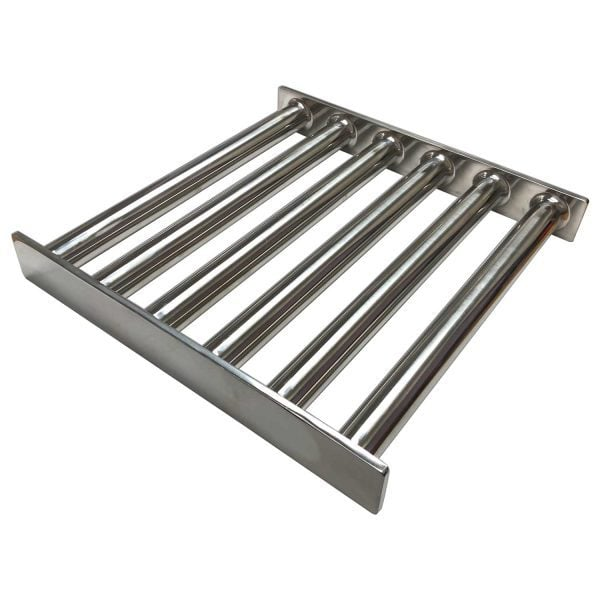
These are the most common design, featuring a single row of magnetic bars within a square, round, or rectangular frame. They are suitable for general applications with light to moderate contamination levels.
Double- or Multi-Layer Grids
In more demanding environments, multi-layer grids provide higher magnetic field density and improved capture efficiency. Particles that pass through the first layer are intercepted by the second, enhancing overall purity.
Circular Grids

Circular magnetic grids are specifically designed to fit hoppers or bins with round openings. Their geometry ensures tight sealing, minimizing bypass and ensuring consistent exposure.
Easy-Clean Grids
In systems where downtime must be minimized, easy-clean magnetic grids feature quick-release bars or sleeves that allow rapid cleaning without disassembly. These are ideal for high-throughput lines or facilities with strict hygiene requirements.
Pneumatic Line Grids
Built for inline installation in pneumatic conveying systems, these magnetic separators are engineered to withstand pressure and air velocity while offering high-strength magnetic separation.
Sanitary/Hygienic Grids
These grids are designed for industries with strict cleanliness regulations, such as pharmaceuticals or dairy processing. They often feature polished surfaces, welded joints with no crevices, and may include protective sleeves that simplify cleaning.
Key Advantages of Magnetic Grids
Magnetic grids offer a wide array of advantages that make them indispensable in many industrial processes.
Equipment Protection
By capturing ferrous particles before they reach sensitive equipment like mixers, grinders, or packaging machines, magnetic grids prevent wear, damage, and costly downtime.
Product Quality
Contaminants not only degrade the quality of the product but can also lead to recalls or consumer complaints. Magnetic grids ensure a higher level of product purity by trapping metallic debris.
Compliance and Safety
Many industries must comply with quality assurance programs such as HACCP, BRC, or ISO 22000. Installing magnetic grids is an effective way to meet metal detection and foreign body control standards.
Ease of Use
Unlike active filtration systems, magnetic grids operate passively with no need for electricity or motors. Maintenance is minimal, cleaning is simple, and operating costs are virtually zero.
Adaptability
Magnetic grids can be custom-built to fit almost any chute, bin, or pipe. Whether you’re handling fine powders, plastic pellets, or large granules, a grid can be tailored to suit your product and process.
Cost-Effective
Though simple in design, magnetic grids are incredibly efficient. Their long lifespan, minimal maintenance, and ability to reduce product loss or equipment repair make them a high-ROI investment.
Performance Indicators
To ensure that a magnetic grid is performing well, users should regularly evaluate several key indicators:
Magnetic Field Strength
This is measured in Gauss. Most standard grids operate at 8,000–12,000 Gauss, but some may reach higher levels. A strong field ensures effective capture of even the smallest ferrous fragments.
Flow Rate and Dwell Time
The slower the material passes over the magnets, the more likely contaminants will be captured. Systems with fast flow rates may benefit from multiple grid layers or baffle designs.
Particle Retention
A grid’s ability to hold onto captured material, especially under vibration or airflow is critical. Poor retention leads to recontamination downstream.
Clean Pull Test
This manual or instrumented test checks the strength of magnetic force using a test object. Decreasing pull strength may indicate aging magnets or damage.
Build-Up and Bridging
Watch for signs of material bridging (blockage) around or above the grid. This could indicate improper sizing, orientation, or an issue with flow consistency.
Installation Best Practices
To get the best performance from a magnetic grid, installation should be carefully planned and executed. Placement, orientation, and system integration all influence effectiveness.
1. Placement in Flow Path
Install grids where materials are flowing slowly or in free fall. The goal is to maximize exposure time between particles and the magnetic field. Ideal locations include hopper outlets, vibratory feeders, or vertical drop sections.
2. Avoid Obstruction
Ensure the grid fits snugly but does not overly restrict flow. Undersized grids may cause bridging or clogging, while oversized ones could allow contaminants to bypass the magnetic field.
3. Angle of Installation
For vertical chutes, flat grids work well. In sloped or horizontal ducts, consider mounting the grid at a slight angle to reduce accumulation and encourage consistent flow across all bars.
4. Pre-Filtration Layer
In dusty or sticky environments, adding a screening or mesh layer upstream helps protect the magnetic grid and reduce buildup. This allows the magnets to work more efficiently.
5. Regular Testing and Adjustment
Periodically inspect the position and alignment of your grids. If material buildup is heavy in one section, repositioning may help balance the load and improve performance.
Correctly installed magnetic grids reduce maintenance issues and ensure long-term contaminant capture. Always consult with your supplier or integrator for system-specific recommendations.
Magnetic Grid Maintenance Guide
Routine maintenance is essential to keep magnetic grids performing at peak levels. Even though they are passive devices, contamination buildup, improper handling, or environmental wear can degrade performance.
1. Scheduled Cleaning
Develop a routine based on production hours or material type. High-dust or high-volume environments may require daily cleaning, while lower-risk applications might only need weekly attention.
2. Safe Handling
Use gloves and caution when handling magnetic grids. The strong magnetic force can attract tools or debris suddenly, posing a risk of pinching or injury.
3. Cleaning Technique
Wipe down bars with a lint-free cloth and non-corrosive cleaner. Avoid scrubbing with steel wool or abrasive materials that could scratch stainless steel surfaces.
4. Magnet Condition Checks
Visually inspect rods for dents, cracks, or discoloration. These may indicate internal magnet degradation. If a magnet loses strength, it should be replaced immediately.
5. Use of Sleeves or Covers
In food or pharma facilities, rods may be encased in plastic or Teflon sleeves to simplify cleaning. Be sure to check for sleeve damage and sanitize according to protocol.
6. Documentation
Keep a cleaning and inspection log for audits and compliance. Record any repairs, replacements, or performance tests for traceability.
A well-maintained magnetic grid will last for years, reduce risk, and continue delivering the contaminant control you rely on.
Case Studies & Real-World Examples
Food Processing – Removing Metal from Spices
A leading spice manufacturer faced issues with fine metal fragments appearing in their ground pepper batches. Despite sieves and visual checks, complaints from retailers persisted. By installing double-layer magnetic grids at the exit of their milling system, the company eliminated nearly all trace contaminants. Product complaints dropped by 97%, and they passed their next food safety audit with zero non-conformances.
Plastic Pellet Manufacturing – Protecting Extruders
A plastics supplier producing high-grade pellets experienced frequent clogging in their extrusion lines. Microscopic metal flakes were damaging nozzles and reducing output quality. After integrating rectangular magnetic grids at the drying stage, they reduced unscheduled shutdowns by 60%. ROI was achieved in less than four months.
Pharmaceutical Packaging – Ensuring Clean Capsules
A pharma plant handling powdered medication used magnetic grids to safeguard capsule filling machines. During validation, metal shavings from upstream mechanical wear were discovered. After retrofitting pneumatic line magnetic grids, the company recorded a 100% drop in metal detection alarms downstream. They now include grid maintenance as part of GMP protocol.
These examples show the adaptability of magnetic grids to vastly different sectors, materials, and challenges.
Emerging Innovations in Magnetic Grid Technology
The future of magnetic filtration is evolving. Manufacturers are pushing the boundaries of how smart and adaptable magnetic grids can become.
Smart Magnetic Grids
With embedded sensors and digital monitoring, smart grids can alert operators to cleaning needs, performance drops, or potential failures. Integration with SCADA or IoT systems allows predictive maintenance and data logging.
Variable-Field Designs
New bar technologies allow magnetic field strength to vary along the length of a rod, offering optimized capture zones for mixed particle sizes.
Hybrid Filters
Some new systems combine magnetic bars with screens or sieves in a single unit, enabling dual-mode filtration in one compact housing. These save space and offer broader contaminant removal.
Sanitary Enhancements
Advancements in coatings, weld polishing, and self-draining frames are raising the hygiene standard, particularly for biotech and cleanroom applications.
These innovations represent the next step in magnetic separation boosting efficiency, improving data visibility, and reducing operator intervention.
Final Thoughts
Magnetic grids may seem like a small part of your system, but their impact is huge. From catching stray metal before it damages your equipment to helping you stay compliant with strict purity standards, they are one of the smartest, simplest upgrades you can make.
Whether you need a standard model or a custom-engineered grid, the right solution will reduce risk, improve product quality, and streamline operations. They bring together strength, simplicity, and silent efficiency in a form that works reliably day after day.
Browse 뉴랜드 매그네틱스 to explore our magnetic grid lineup or get a quote tailored to your specific application.
A well-designed magnetic grid doesn’t just protect product it preserves your brand reputation, supports operational efficiency, and keeps your facility running at its best. In tod