Table of Contents
Magnetic powder plays a vital role in modern industries, serving diverse applications, from electric motors and transformers to magnetic sensors, medical devices, and data storage solutions. Technological changes have increased the demand for high-performance, reliable, and customizable magnetic materials.
There are too many varieties of magnetic powders, each with characteristics ranging from compositional differences to strength, thermal stability, and electrical properties. Such differences in composition, strength, thermal stability, and electrical properties render the act of selecting the best difficult.
If you are into advanced electronics, automotive manufacturing, or high-frequency component engineering, one has to understand the properties and classifications of magnetic powder. In this informative guide, you will study magnetic powder, what it’s made of, its properties, and its uses in diverse areas. Continue reading, so you can confidently select the magnetic powder you require.
Part 1: What is magnetic powder?
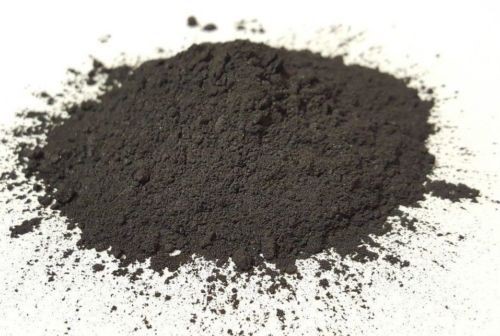
The term applied to magnetic powders refers to fine powders that exhibit such magnetic properties as magnetization, remanence, and coercivity. The powders essentially constitute raw materials used for manufacturing different magnetic products such as permanent magnets, soft magnetic cores, magnetic recording media, and electromagnetic shielding materials.
Going deep, the primary advantage of magnetic powder is its versatility. It can be compressed into solid forms, mixed with binders to produce bonded magnets, or suspended within polymers or coatings for flexible magnetic applications.
Particle size ranges from nanometers to about a couple of microns, depending on the application. This reduction in particle size, however, increases the surface area-to-volume ratio, higher magnetic performance, and improved processing behavior.
Magnetic powders can be broadly divided into two categories: the hard and the soft magnetic powders. Whereas the soft magnetic powders get magnetized and demagnetized easily and therefore find use in transformers, inductors, and the like, soft magnetic powders retain magnetization and are employed as permanent magnets in motors, generators, and sensor applications.
Most common powders of material used are pure iron and iron alloys, ferrites (the ceramic oxides), and the rare earth compounds-neodymium-iron-boron (NdFeB) and samarium-cobalt (SmCo). Each one of these has its distinct properties and pros.
Part 2: What Material is Magnetic Powder Made Of?
The production of magnetic powder may be done in a wide manner, depending on the materials used, each being tailored for certain performance and application needs. The magnetic force, heat protection, electricity, and anti-corrosion characteristics change according to the composition used.
Principally, these are elemental metals, ceramic compounds, and rare-earth alloys as material classes for magnetic powder manufacturing. They include:
Iron and Iron-Based Alloys
Iron is a very common magnetic powder with very good saturation magnetization and low cost. Apart from being susceptible to corrosion, it is generally alloyed with other elements:
- Silicon (Fe-Si): To raise electrical resistivity and reduce eddy current losses so that it can be used for high-frequency applications.
- Nickel (Fe-Ni): For high permeability and low core losses to be used in the manufacture of precision electronics and magnetic shielding.
- Cobalt (Fe-Co): For improved magnetic performance and temperature stability to be used in aerospace and defense.
Ferrites
Ferrites are ceramic compounds prepared by mixing iron oxide (Fe₂O₃) with oxides of other metals such as manganese, zinc, or nickel. Being electrically non-conductive, these materials are suitable for high-frequency applications in which eddy currents are greatly reduced. These powders find uses mostly to manufacture magnetic cores for transformers, inductors, and EMI filters.
Magnetic Rare-Earth Alloys
End users looking for high-performance, small applications turn to rare-earth magnets since they always produce the highest energy magnetic characteristics.
Neodymium-iron-boron (NdFeB) alloy has the strongest magnetic qualities known to man. Consumer electronics, wind turbines, and strong motors use this magnet.
Others go for Samarium-Cobalt (SmCo). Due to its extraordinary corrosion resistance and thermal stability, the SmCo magnet is employed in military, aerospace, and high-temperature environments.
Alnico (aluminium, nickel, and cobalt)
Older technology alnico powders are still used in sectors including electric guitar and measuring instruments, where high-temperature stability and mechanical strength are needed.
Part 3: What Are the Main Characteristics of Magnetic Powder?
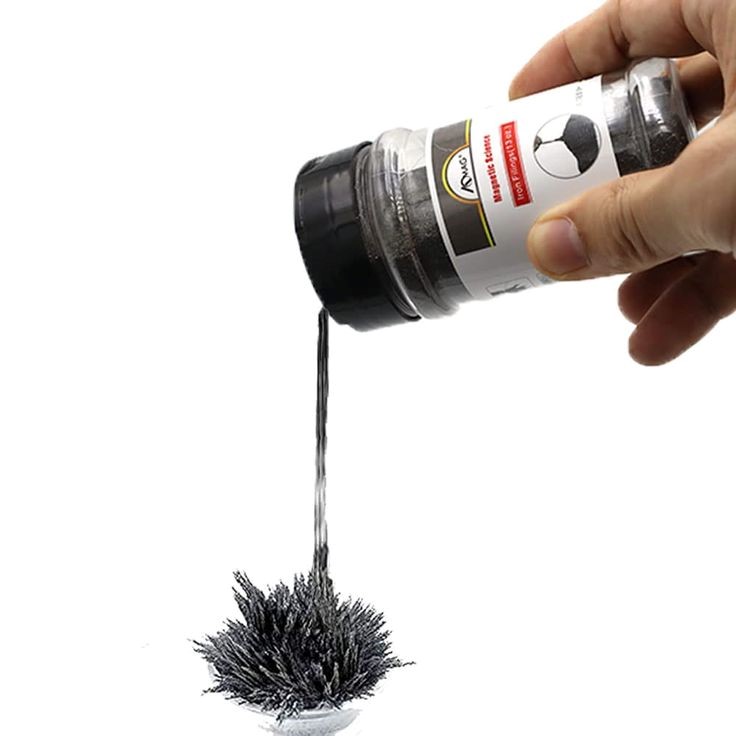
The following are the primary properties of magnetic powder:
Magnetic Properties
a. Saturation Magnetization (Ms)
This is the maximum magnetization that a material can have in response to an external magnetic field. The higher the saturation magnetization, which represents a stronger magnetic property, the better for motors and magnetic assembly. The extremely large values of Ms are usually found in the NdFeB and Fe-Co alloys.
b. Coercivity (Hc)
The resistance of a material to becoming demagnetized is known as coercivity. High coercivity hard magnetic powders like NdFeB and SmCo are perfect for permanent magnets. Conversely, soft magnetic powders like ferrites and Fe-Si have low coercivity and are meant to magnetize and demagnetize swiftly for AC use.
c. Remanence (Br)
Remanence is the magnetization a material retains after the outside magnetic field is turned off. Permanent magnets where retaining magnetism is important need high Br values.
d. Magnetic permeability
This is the degree to which a material can be magnetized—that is, its magnetizability. For cores in inductors and transformers, high permeability enables effective magnetic flux conduction; therefore, high permeability is essential.
Particle Size and Distribution
Usually ranging from nanometers to several micrometers, magnetic powder particles fulfill this criterion. In bonded magnets, smaller particles provide greater surface area, improved sintering performance, and more homogeneity. Uniform particle size distribution helps to ensure constant magnetic performance and processing effectiveness.
Electrical resistivity
Particularly in high-frequency uses, electrical resistivity is a critical component in minimizing current losses. High resistivity of materials like ferrite makes them ideal for inductors and transformers. To decrease energy loss during fast switching, iron-based powders are sometimes coated or alloyed to increase resistivity.
Thermal Stability
Certain uses demand dependable performance of magnetic powders at elevated temperatures. Materials like SmCo and Alnico show amazing thermal stability since they preserve magnetic characteristics even over 250°C. Particularly in automotive and aerospace systems, thermal stability influences long-term reliability as well.
Resistance to Corrosion
Particularly in wet or chemically hostile surroundings, corrosion can seriously compromise magnetic performance. Natural corrosion resistance exists in ferrites; rare-earth magnets like NdFeB may need surface coatings (e.g., nickel, epoxy) to guard against oxidation.
Mechanical Qualities
Magnetic powder’s brittleness, hardness, and mechanical strength could influence its application and processing. For example, ductile powders are simpler to mold and press into complex forms, but brittle materials could fracture during compacting or machining.
Compatibility with binders
In bonded magnet uses, the powder has to go along with organic or synthetic binders. This influences the general performance of the magnet and determines how effectively the powder distributes in the matrix.
Part 4: What Are the Main Classifications of Magnetic Powder?
Usually, magnetic powders are grouped according to their magnetic behavior, structure, and composition. Soft magnetic powders and hard magnetic powders are two main classes; both find different uses in technical and industrial contexts. Let us investigate these categories in more depth:
Soft Magnetic Powders
Materials called soft magnetic powders easily magnetize when an outside magnetic field is applied and lose their magnetism after the field is withdrawn. Alternating current (AC) uses, where fast magnetization and demagnetization are needed, call for these powders.
Common Soft Magnetic Materials:
- Iron Powder (Fe)
- Silicon Steel Powder (Fe-Si)
- Iron-Nickel Alloys (Fe-Ni)
- Ferrite Powder (Mn-Zn, Ni-Zn)
Key Characteristics
- Low coercivity
- High magnetic permeability
- Low core losses at high frequencies
- Moderate saturation magnetization
Typical Applications
- Transformers and inductors
- Electromagnetic coils
- Magnetic shielding
- Chokes and filters
Hard Magnetic Powders
Hard magnetic powders, also known as permanent magnetic powders, retain magnetization even after the external magnetic field is removed. These materials are critical in applications that require long-term magnetism and high energy density.
Common Hard Magnetic Materials
- Neodymium-Iron-Boron (NdFeB)
- Samarium-Cobalt (SmCo)
- Alnico (Aluminum-Nickel-Cobalt)
- Hard Ferrites (Strontium or Barium Ferrite)
Key Characteristics
- High coercivity
- High remanence
- Excellent temperature and corrosion resistance (depending on the type)
- Suitable for miniaturized and high-power devices
Typical Applications
- Motors and generators
- Magnetic sensors and actuators
- Wind turbines
- Consumer electronics
- Medical devices (e.g., MRI machines)
Bonded vs. Sintered Magnetic Powders
Magnetic powders can also be classified by processing method:
- Bonded Powders: Mixed with binders (resin or polymer) and pressed into shape. Offer complex geometries and lower cost.
- Sintered Powders: Compacted and heated at high temperatures for dense, high-performance magnets.
Part 5: Which fields can use magnetic powder?
Magnetic powder is a basic material used in various industries given its flexible magnetic properties, easy processing, and fit for various application needs. From consumer electronics to renewable energy, magnetic powders support innovation, miniaturization, and performance enhancement across several industries.
These are the primary sectors utilizing magnetic powder much:
Telecommunications and Electronics
All inductors, transformers, EMI filters, and magnetic shielding devices rely on magnetic powders. Especially valued for their high-frequency performance and electrical insulation qualities, ferrite and iron-based powders help reduce power loss and improve signal integrity in circuit boards, routers, and gadgets such as smartphones.
Automotive Industry
Particularly rare-earth kinds like NdFeB, the move to electric vehicles (EVs) and hybrid technologies has considerably boosted demand for high-performance magnetic powders. Used in electric motors, actuators, sensors, and magnetic brakes, these powders help modern cars’ efficiency, power density, and lightweight design by
Energy and Power Generation
Hard magnetic powders like NdFeB and SmCo are essential for producing strong and small permanent magnets in wind turbines and generators. In transformers and inductors for energy transmission and conversion, soft magnetic powders are used, with Low core losses and great permeability, boosting energy efficiency of power systems.
Medical and Health Care
In cancer treatment, magnetic hyperthermia therapy uses magnetic powders; in drug delivery systems, biosensors, and medical imaging (such as MRI machines), they have particular uses. Their excellent, non-invasive applications depend on their biocompatibility, strong magnetic response, and fine particle size.
Aerospace and Defense
In aerospace and military applications, magnetic powders are found in high-performance motors, navigation systems, and sensors. Preferred for their thermal stability and corrosion resistance, SmCo and Alnico powders guarantee successful operation under hostile environments.
Part 6: Which magnetic powder brands are worth choosing?
Newland Magnetics
Newland Magnetics stands as a reliable entity within the magnetic material sector, focusing on premium magnetic powders and bonded magnets. Through its extensive research background and industry experience, Newland delivers an extensive assortment of products, including NdFeB powder, ferrite powder, and injection-molded magnetic materials.
The application of their powders spans electric motors, automotive components, electronics, and energy systems. Through its unique customization capabilities combined with competitive pricing and sustainable practices, Newland Magnetics emerges as a preferred supplier for manufacturers of all scales across the globe.
Hitachi Metals
Hitachi Metals emerged as a leader in rare-earth magnet production and, now operating under Proterial Ltd., it gained fame for its exceptional NdFeB magnetic powders. Their powders incorporate superior quality standards and patented technologies, which render them apt for sophisticated automotive and industrial applications.
Arnold Magnetic Technologies
Based in the U. S. Arnold manufactures an extensive range of magnetic materials that includes both rare-earth elements and bonded magnetic powders. The aerospace, defense, and medical device sectors extensively utilize their materials, which are renowned for exceptional precision and durability.
VACUUMSCHMELZE (VAC)
VAC represents a globally active German enterprise that focuses on producing both soft and hard magnetic powders. Their products find application in high-efficiency transformers, inductors, and electric motors, specifically where high thermal stability demands exist.
Conclusion
Magnetic powder functions as a fundamental component across numerous contemporary technologies by serving as a multipurpose material essential for electric motors, transformers, medical devices, and consumer electronics.
An understanding of composition alongside characteristics and classifications enables businesses and engineers to make sound decisions regarding magnetic powder selection for their specific needs. Through partnerships with dependable suppliers such as Newland Magnetics, businesses access premium materials alongside tailored solutions and specialized assistance.
Regardless of your industry, whether automotive, energy, healthcare, or electronics, choosing the appropriate magnetic powder boosts product and system performance along with efficiency and innovation. With your newfound knowledge, selecting the appropriate magnetic powder becomes a pivotal factor that can transform your long-term success.