Tabla de contenido
Drop-shaped magnets might look simple at first glance, but they play a surprisingly versatile and critical role in countless industries. Shaped like a water droplet or teardrop, these magnets combine form and function in a compact, aerodynamic design.
In this comprehensive guide, we’ll walk through what drop-shaped magnets are, how they’re made, their various types, key benefits, top applications, and how to evaluate their quality. Whether you’re a product designer, engineer, buyer, or just curious about industrial magnets, this guide is built to inform and help you make smarter decisions.
What is a Drop-shaped Magnet?
A drop-shaped magnet is a permanent magnet formed in the shape of a teardrop or droplet. This unique geometry provides focused magnetic force at the tip while maintaining smooth contours for controlled use in specialized applications.
These magnets are engineered to concentrate their magnetic field at the tapered end, allowing for high precision in tasks where controlled magnetic interaction is critical. This shape not only offers aesthetic advantages but also provides functionality in confined or dynamic environments.
Often used where alignment, precision, or aerodynamic properties are important, drop-shaped magnets are both functional and visually distinct. They are usually crafted from neodymium, ferrite, or samarium-cobalt materials, depending on the strength and temperature needs of the application.
The drop shape also contributes to better handling and ease of integration into non-linear or curved components. Their unique profile makes them suitable for magnetic couplings, sensors, and devices where directional magnetism is crucial.
How Are Drop-shaped Magnets Made?
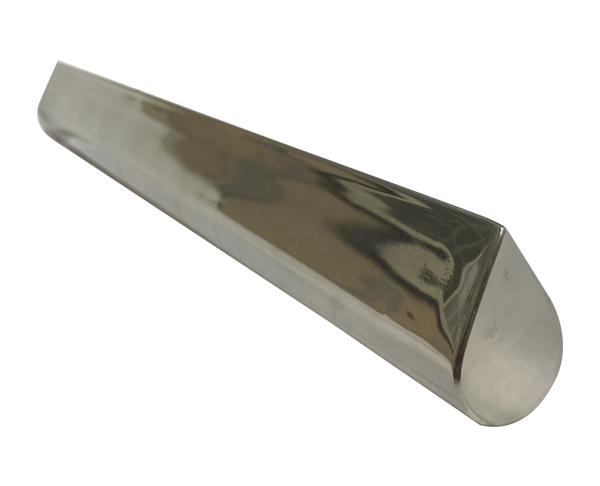
Manufacturing drop-shaped magnets requires a blend of precision forming, magnetizing, and quality control. The process begins by selecting the appropriate magnetic material—commonly neodymium iron boron (NdFeB) for high strength or ferrite for cost-effective performance.
The chosen material is typically milled into fine powder and pressed into drop-shaped molds under high pressure. These molded forms are then sintered at high temperatures to bond the particles and give the magnet its solid structure.
The raw material is cast or pressed into shape using molds specifically designed for the drop profile. Then comes the sintering process, where the magnet is heated to near melting point to harden and align magnetic particles.
After sintering, the magnets may be machined to achieve tight tolerances. This step ensures dimensional precision, especially in the tapered tip, which affects the magnet’s performance. Surface smoothing is often done before coating.
Once sintered, the magnet undergoes machining to perfect its contours. Coating is applied afterward to prevent corrosion, typically using nickel, epoxy, or a custom coating suited to the environment. Finally, the magnet is magnetized and tested under strict conditions to ensure consistency, strength, and reliability.
Each finished magnet is then subjected to a magnetizing field that aligns its domains and gives it permanent magnetic properties. Quality assurance tests, including pull force and dimensional accuracy, are conducted before packaging.
Types of Drop-shaped Magnets
Neodymium Drop-shaped Magnets
These are the strongest and most popular, offering powerful magnetic force in a compact form. Ideal for precision tasks, electronics, and compact devices where high magnetic strength is critical.
Their small size allows them to be embedded into tiny components without sacrificing pull force. They are widely used in medical instruments and audio devices.
Neodymium magnets have excellent magnetic properties but require proper coatings to resist corrosion. Common coatings include nickel, zinc, and epoxy.
Ferrite Drop-shaped Magnets
Ferrite versions are more affordable and resistant to demagnetization. They are common in bulk or consumer applications that don’t require extreme strength but benefit from stable performance.
These magnets are also resistant to corrosion and perform well in humid or wet environments, making them ideal for outdoor or utility products.
Ferrite magnets can operate at higher temperatures than neodymium but have a lower magnetic energy product, making them better suited for low-force applications.
Samarium-Cobalt Drop-shaped Magnets
These magnets excel in high-temperature environments and offer strong corrosion resistance. Often used in aerospace or high-performance machinery, they combine reliability with long-term durability.
Though more expensive, they’re ideal for critical applications where performance cannot be compromised by heat or wear.
They also maintain magnetic stability under radiation and are used in defense and space technologies where extreme conditions are common.
Coated Drop-shaped Magnets
These magnets are given protective finishes such as nickel, zinc, rubber, or epoxy. Each coating serves a specific purpose, such as preventing corrosion, improving grip, or blending with external components.
The choice of coating depends on environmental exposure, required aesthetics, and mechanical wear resistance.
Custom coatings may include Teflon or gold for medical-grade applications, ensuring compatibility with human tissue or harsh sterilization cycles.
What Are the Advantages of Drop-shaped Magnets?
Focused Magnetic Strength
The tapered end concentrates the magnetic field at the point, offering precise control. This is particularly useful for magnetic sensors, closures, or pinpoint holding applications where directionality matters.
Their shape allows them to interact more predictably with magnetic circuits, improving efficiency in targeted operations.
In electronics, this focused force is essential when working in tight enclosures where only part of the magnet is exposed or active.
Streamlined Design
The aerodynamic shape is suitable for designs where appearance or fluid dynamics matter, such as in medical tools, robotics, or drones.
It also reduces air or fluid resistance in moving systems, making them a preferred option for integration in motion-sensitive devices.
Their low drag and ergonomic form factor help reduce friction and noise in mechanical assemblies or airflow applications.
Versatility Across Materials
Drop-shaped magnets can be manufactured using various base materials. This allows engineers to select the right combination of magnetic strength, temperature stability, and cost.
It also makes them adaptable for projects ranging from mass-market consumer products to precision engineering components.
Material versatility ensures compatibility with diverse applications, from underwater sensors to cryogenic robotics.
Durable and Long-Lasting
With the right coating, drop-shaped magnets resist corrosion and wear, even in demanding environments. This makes them a good long-term investment.
They can perform reliably over years of use, especially in sealed or sensitive assemblies.
Durability under load and in harsh temperatures enhances their usefulness in military and automotive components.
Easy Integration
The drop profile fits easily into molded parts, cavities, or housings. This makes it ideal for embedded or discreet installations where space and shape constraints matter.
Their geometry also helps them stay seated in curved or slotted housings, reducing the need for complex fixtures.
They’re also easier to align in polarized assemblies, reducing errors during installation and assembly line procedures.
Applications of Drop-shaped Magnets
Electrónica de consumo
Used in wireless charging docks, earbud cases, and magnetic closures, these magnets support smooth function in compact designs.
Their shape allows for controlled magnetic interaction, which is important in delicate electronics that require both power and precision.
Drop-shaped magnets also appear in laptop covers, smartphone mounts, and detachable accessories due to their reliability and clean aesthetics.
Dispositivos médicos
Their smooth, tapered shape is preferred in surgical tools, imaging accessories, and even implantable devices. The non-invasive design supports hygiene and safety.
Drop-shaped magnets are also easier to coat with biocompatible materials, making them ideal for medical environments.
Applications include endoscopic devices, MRI-compatible fixtures, and drug delivery systems.
Aerospace and Automotive
In aerospace systems, drop-shaped magnets help optimize space and weight while delivering precise performance. They are used in sensors, motor components, and aerodynamic housings.
In the automotive sector, they can be found in advanced driver assistance systems (ADAS), electric motors, and battery enclosures.
They also serve as alignment elements in actuators and electronic control units where vibration tolerance is critical.
Industrial Equipment
These magnets are applied in magnetic clamps, fasteners, and pick-and-place tools. Their focused pull is valuable for automation and high-speed assembly.
They are also useful in inspection tools, where their geometry helps operators reach tight or confined areas.
In robotics and CNC systems, drop-shaped magnets enable precision positioning and smart locking mechanisms.
DIY, Crafts, and Design
Crafters and designers use drop-shaped magnets for elegant yet functional magnetic closures, displays, and modular structures. Their design adds a refined aesthetic element.
They are easy to integrate into creative projects, from wearable tech to interactive models and retail packaging.
Designers also favor them for furniture latching systems and interactive product demonstrations.
Important Indicators for Testing the Quality of Drop-shaped Magnets
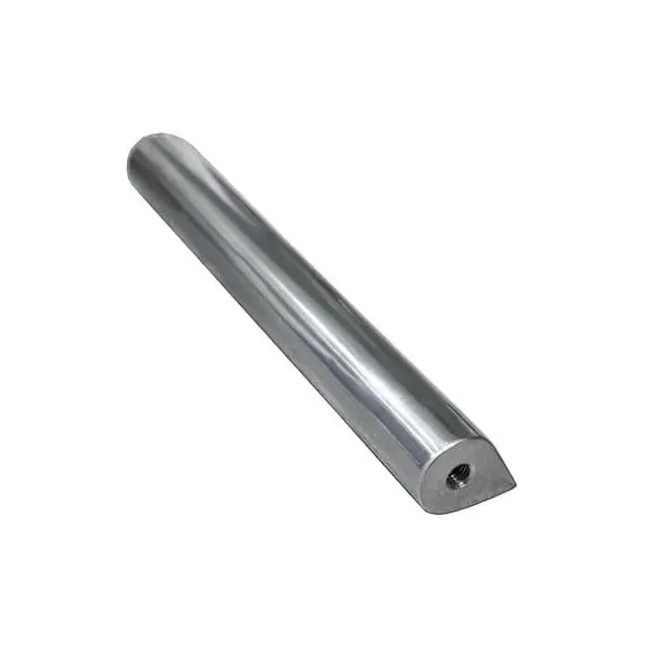
Magnetic Field Strength (Gauss Level)
Verify the magnet’s field intensity to ensure it meets your application’s requirements. This measurement reflects how much force the magnet can exert at a given point.
Always test the magnetic surface for strength uniformity, especially at the tip, which is often the critical contact point.
Using a gaussmeter during batch testing ensures compliance with safety and performance specifications.
Dimensional Accuracy
The unique shape must be machined with high precision. Any deviation can lead to performance issues or misfits during assembly.
Use digital calipers or 3D scans to verify all dimensions, especially the tip radius and taper angle.
Maintaining dimensional consistency helps in automated installations and product scalability.
Coating Durability
Check for chipping, flaking, or inadequate thickness that could lead to corrosion over time. Coatings should pass salt spray and abrasion tests.
The quality of the coating affects both performance and lifespan, especially in humid or reactive environments.
In critical applications, additional testing like thermal cycling or immersion is recommended.
Tolerancia de temperatura
Ensure the magnet material suits the thermal environment. Neodymium, for instance, can degrade under heat unless properly rated.
Review the max working temperature on technical datasheets and compare with real-world conditions in your use case.
Samarium-cobalt magnets are preferable in high-heat or high-altitude environments.
Pull Force Consistency
Every unit should demonstrate consistent holding power. Variations can lead to assembly issues or uneven product performance.
Conduct batch pull tests to confirm each magnet meets the specified pull strength within tolerance.
This is especially important in safety-critical assemblies where magnetic force serves a locking or retention role.
Magnetic Orientation
Correct polarity and alignment are critical. Misalignment can ruin performance in sensitive assemblies and magnetic circuits.
Use a polarity checker to verify that each magnet is aligned and oriented according to your design specifications.
Consistent orientation ensures performance predictability and reduces sorting or rejection during assembly.
Where to Import Drop-shaped Magnets?
Porcelana
China is the leading manufacturer and exporter of rare-earth and ferrite magnets. You’ll find a wide range of drop-shaped options at competitive prices and scalable volumes.
Suppliers often offer customization services, allowing you to define magnet grade, coating, and packaging preferences.
Chinese manufacturers support bulk orders and often include global certifications such as RoHS, REACH, and ISO.
Germany & Japan
Both countries focus on high-precision and custom-engineered magnets. Their manufacturing standards are ideal for demanding industries like automotive, robotics, or aerospace.
These suppliers may come at a premium but deliver consistent, certified, and highly engineered products.
German and Japanese manufacturers are preferred where long-term reliability and low deviation in batch production are essential.
USA
U.S.-based manufacturers offer quick turnaround and strong technical support. They’re best for low-volume, high-precision projects or where compliance and customer service are key.
Ideal if you need rapid prototyping or local testing for regulatory approvals.
Many U.S. suppliers provide engineering consultation and fast customization for R&D or defense projects.
Why Choose Newland Magnet?
At Newland Magnet, we specialize in precision-engineered magnetic solutions, including high-quality drop-shaped magnets. We offer a wide range of materials, coatings, and custom services tailored to your exact needs.
Whether you’re designing medical equipment, sourcing parts for industrial automation, or prototyping the next big consumer product, we can support you from concept to delivery. Quality, consistency, and expert support are what set us apart.
To explore our capabilities or request a quote, visit us at https://www.newlandmag.com/.
Final Thoughts
Drop-shaped magnets offer more than just a sleek appearance. Their shape allows for targeted magnetic strength, compact integration, and flexible applications across many industries.
From high-tech devices to everyday consumer products, these magnets quietly support performance, durability, and smart design. Their aerodynamic and functional advantages make them a standout choice for engineers and designers alike.
If you’re evaluating your next magnet supplier or project specs, include drop-shaped magnets in your shortlist. They offer unique advantages that may solve design or performance challenges more efficiently than conventional options.